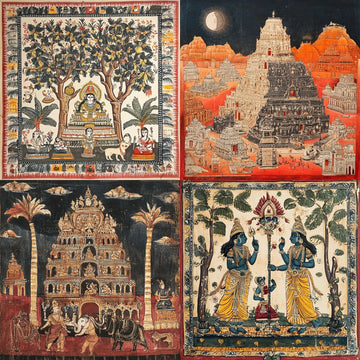
Kalamkari is more than just a craft. It's a celebration of tradition, where no chemicals or machines are used, only the skillful hands of artisans and the vibrant hues of natural dyes. It is usually done on cotton fabrics using only vegetable dyes or natural colors. The artisans use bamboo pens, date palms, and tamarind sticks to work their magic on cotton fabric.
But here's the juicy part: Kalamkari isn't just one style—it's got two flavors: Srikalahasti and Machilipatnam. Each has its own unique vibe and design flair, ready to captivate your imagination.
In Srikalahasti style, intricate borders and detailed storytelling are the hallmarks. Religious myths, epic tales, and even a sprinkle of Persian influence, thanks to the Mughals and Golconda Sultanate, are also present.
On the other hand, the Machilipatnam style takes a different route. It's all about block printing and Persian vibes. It has floral patterns, tribal art, and scenes from everyday life.
But wait, there's more! Let's break down the nitty-gritty of how Kalamkari gets made, step by step.
Ever wondered what goes into creating those gorgeous Kalamkari prints? It's quite a journey! The skilled artisans start by designing intricate patterns on paper. These designs come to life as they're carved into wooden blocks by hand. But that's just the beginning! The canvas for these prints is pure cotton fabric. But before it's ready for printing, it undergoes a thorough process. First, it undergoes a natural treatment with water and cow dung to bleach and remove starches. Then, it is rinsed in a river's running water.
Once sun-dried, the fabric gets another special treatment—a dip in a solution made from myrobalan seeds and buffalo milk. This gives the fabric its off-white base and acts as a natural fixative for the dyes to come. Plus, the milk helps control how the dye spreads on the cloth. The Srikalahasti style is all about treating that fabric like royalty.
After more drying in the open air, it's finally time for the printing magic to happen! Typically, the outline is printed first, often in striking black or red. Then, depending on the designer's vision, colors like red, blue, yellow, green, or black are added. Once the printing is done, it's back to the river for a quick wash to remove any excess dye. And you guessed it—more sun-drying follows. After several rounds of washing and drying, the fabric is finally ready to flaunt its vibrant Kalamkari patterns. It's like crafting your stamp collection, but it's way more artsy.
And just like that, you've got a beautiful piece of Kalamkari art. It's a labor of love, a dance of tradition and creativity passed down through generations. And in a world where sustainability is all the rage, Kalamkari's natural, chemical-free approach is making waves in the textile scene. It demonstrates the enduring significance of art, tradition, and sustainability in today's world.
Inspiration: Pure Mitti, The Design Cart, Prosperity Mirra, Exotic India.